Every year, Mining Magazine celebrates excellence in the mining industry by inviting our readers to nominate people, companies, projects and technologies that they feel have demonstrated outstanding commitment to advancing the state of play in mining over the past 12 months. The shortlisted candidates are then put to the vote.
Congratulations to this year's winners, who are listed below; and thank you to our readers, who took the time to nominate and vote for them.
And the winners are:
Environmental Stewardship:Metso Chile
Metso Chile has been successful in meeting its goal of an annual reduction of 7% of its carbon footprint by 2030, with outstanding performance in 2023 leading to a reduction of 11% CO2 equivalent from January to October. This is due to a diverse series of initiatives, for example, the use of technology such as photovoltaic panels for the generation of renewable electrical energy and the recycling of worn mill liners. Aspects that have to do with the organisational culture and commitment of collaborators in caring for the environment were also important, such as holding events for stakeholders with sustainability challenges, or, for example, through the reuse and revaluation of clothing items, as raw material for the production of reusable bags and new clothing such as caps and therapeutic cushions.
Editor's Choice:Codelco's Andina Division & Metso
In 2023, a successful major maintenance project focused on the molybdenum and copper filtration plant's core filter was carried out at the Andina Division. This initiative, driven by a collaboration between specialists from Codelco and Metso, concluded in record time, under completely safe and sustainable conditions. The initiative resulted in the equipment regaining its efficiency, a key factor for the mining operation. This filtration equipment processes 80% of the site's fine copper production, being one of the largest filters in Chilean mining, with a total of twenty-four filter plates, and a filtration capacity exceeding one hundred tons per hour.
Minerals Processing: (Organisations)Vale and Weir Minerals
Vale and Weir Minerals pioneered the use of the Cavex® 2 CVD hydrocyclone in iron ore desliming application and achieved a 9 percentage point gain in mass recovery, increasing it to 56%.
Vale and Weir Minerals partnered to optimise the desliming stage at Vale's Vargem Grande 2 Plant (VGR2), located near the town of Nova Lima in the state of Minas Gerais, Brazil. The average iron ore slimes losses at VGR2 corresponded to approximately 18% by weight of the total iron ore mined, totalling 1.9 million tons of iron lost every year.
Minerals Processing: (Individuals)Dr. John Forster
John Forster made key advances in the pretreatment of ores to reduce comminution energy and the carbon footprint of mining.
Safety: Hexagon
The HxGN MineProtect Operator Alertness System (OAS) is a leading-edge solution that combines an in-cab device, sensor technology, machine-learning image processing, and advanced algorithms developed by Hexagon to detect and manage risks of operator fatigue and distraction, one of the leading causes of mine accidents. The solution also offers timely interventions and supports continuous operational improvement by connecting onboard technologies with a cloud service for real-time notifications and data analytics.
Fleet Excellence: Liebherr R 9300
The R 9300 is Liebherr Mining's latest addition to its excavator portfolio. This machine takes efficiency to a new level thanks to the latest Liebherr Mining technology embedded. This technology provides the machine with improved onsite performance as well as compatibility with Liebherr's Assistance Systems and future product enhancements such as automation, zero emission technologies, and digital services.
Technology & Innovation: FLSmidth The RFC™- REFLUX™ Flotation Cell
The ability to operate at gas and wash water fluxes above what is traditionally possible with any other existing flotation equipment sets this technology apart.
The REFLUX Flotation Cell (RFC) operates at a magnitude far beyond the capacity of existing flotation devices, reducing the required installation footprint. Its novel arrangement enhances the hydrodynamics of flotation, with the ability to recover a wide size distribution of minerals at a rate of up to 7-10 times faster than traditional methods.
Technology & Innovation (Surface): Orica
Neo is Orica's new brand for environmentally friendly, sustainable initiation systems products. The Neo range of Exel™ non-electric detonators is produced using a lead-free formulation in Gyttorp, Sweden, with no lead or lead compounds used in the manufacturing process of the pyrotechnic delay compositions.
Bulk Handling: Philippi-Hagenbuch
Philippi-Hagenbuch expanded its custom engineering portfolio of HiVol® Hard Rock Bodies to include asymmetrical bodies that are optimized for underground environments. The design maximizes each truck's hauling capacity while allowing for safer, more efficient loading to account for environmental constraints, such as clearance and visibility.
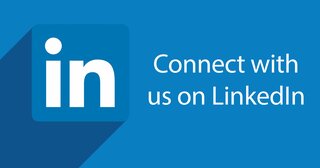