The Swedish original equipment manufacturer (OEM) aims to provide a full electric offering for underground mining by 2025, and electric alternatives to all other models by 2030. So far, those goals remain within reach.
"We have made a number of acquisitions to support the electrification journey and ultimately achieve those bold but ambitious goals of electrification," Epiroc's managing director (Australia), Wayne Sterley, said. Sterley said Epiroc's goals stem from the industry itself, with many mining companies setting their own ambitious targets for electrification.
Epiroc's vice president of electrification, Jerome Cloue, said: "We see increasing adoption and interest from our customers in electric technology, because they can achieve higher productivity and lower cost of ownership, and at the same time reduce their emissions." But while miners have set themselves net zero deadlines, the regional picture is by no means uniform. Some have new fleets up and running while others are only just setting out on their journey.
In South Africa, mining operators using Epiroc's electric 42-tonne trucks have reported productivity gains of about 13%. "It is all related to torque," Sterley explained. "The torque on BEVs is astronomical and the same applies to an underground loader. You are getting better productivity out of the vehicle." Meanwhile in Australia, which Sterley described as "the Texas of mining," larger vehicles including 60-tonne trucks and 22-tonne loaders are slightly more complicated to electrify. "It is taking a bit longer with these vehicles. We do have the technology, but it is going through the final tests and verifications," Sterley said.
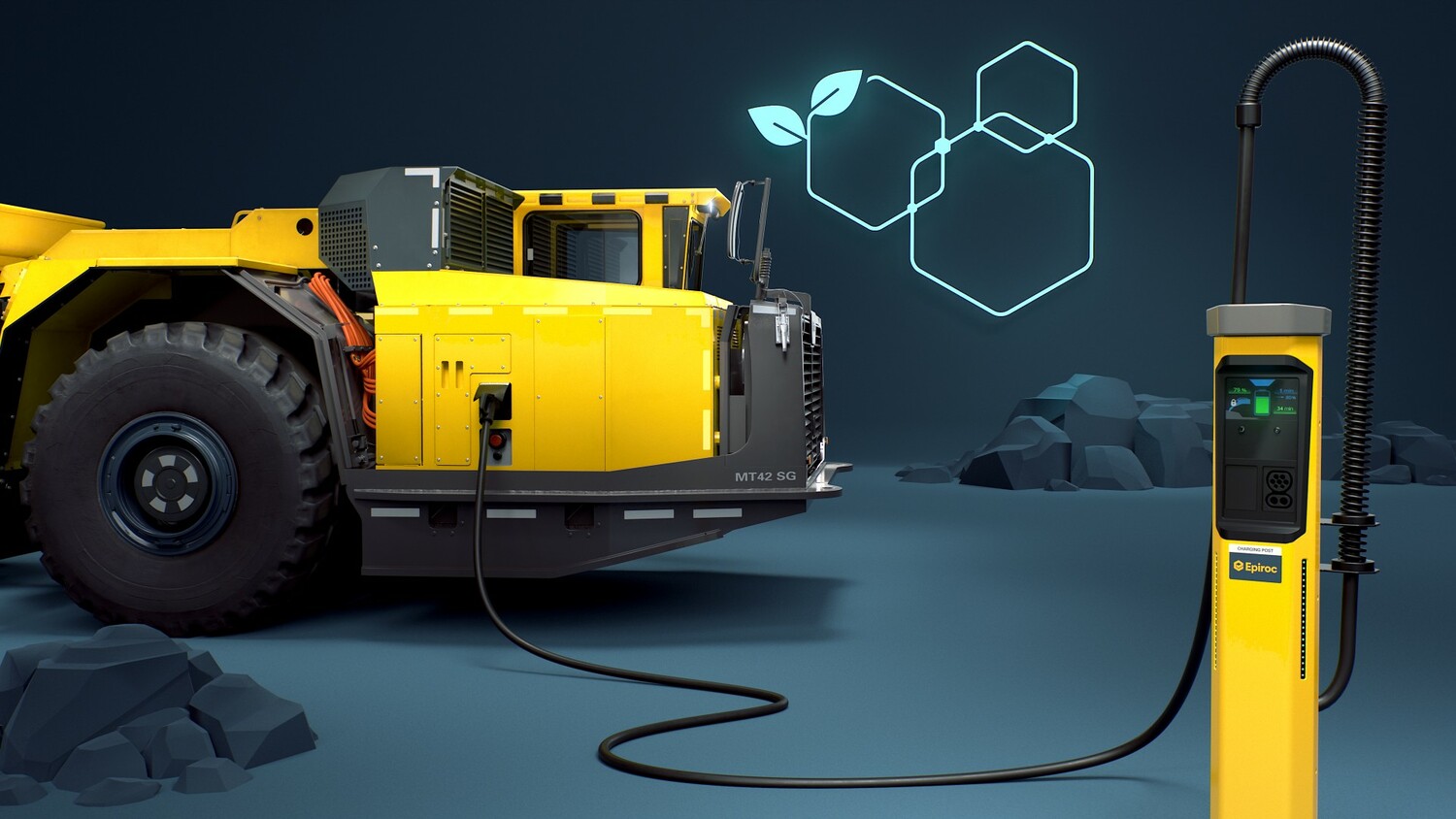
The ease of the process can depend on how the existing mine is set up. "Not all mines are suitably reticulated to accommodate electrification," Sterley added. Epiroc offers a broad range of solutions depending on need and on what stage their customers are at now. These include BEVs, cable electric vehicles, hybrid vehicles, and HVO100-enabled engines, which is a more sustainable type of fuel.
"We see electrification in the mining and construction environment as a journey, and not just a matter of switching from a diesel engine to an electric vehicle," Cloue said. "That is just one factor to consider. A successful journey for our customer depends on their ability to look at that transformation as a full ecosystem."
Epiroc has acquired a portfolio of companies to build expertise in the other parts of this ecosystem, such as energy storage and infrastructure. These include JTMEC in Australia, an infrastructure provider for underground and surface mines. JTMEC's offerings include high voltage installation and maintenance, transformer servicing and testing, and it also manufactures some products including substations and mine chargers. Epiroc has also acquired Meglab, a Canadian technology integrator for infrastructure, and FVT Research – also in Canada – a company with expertise in converting diesel-powered mining machines into BEVs.
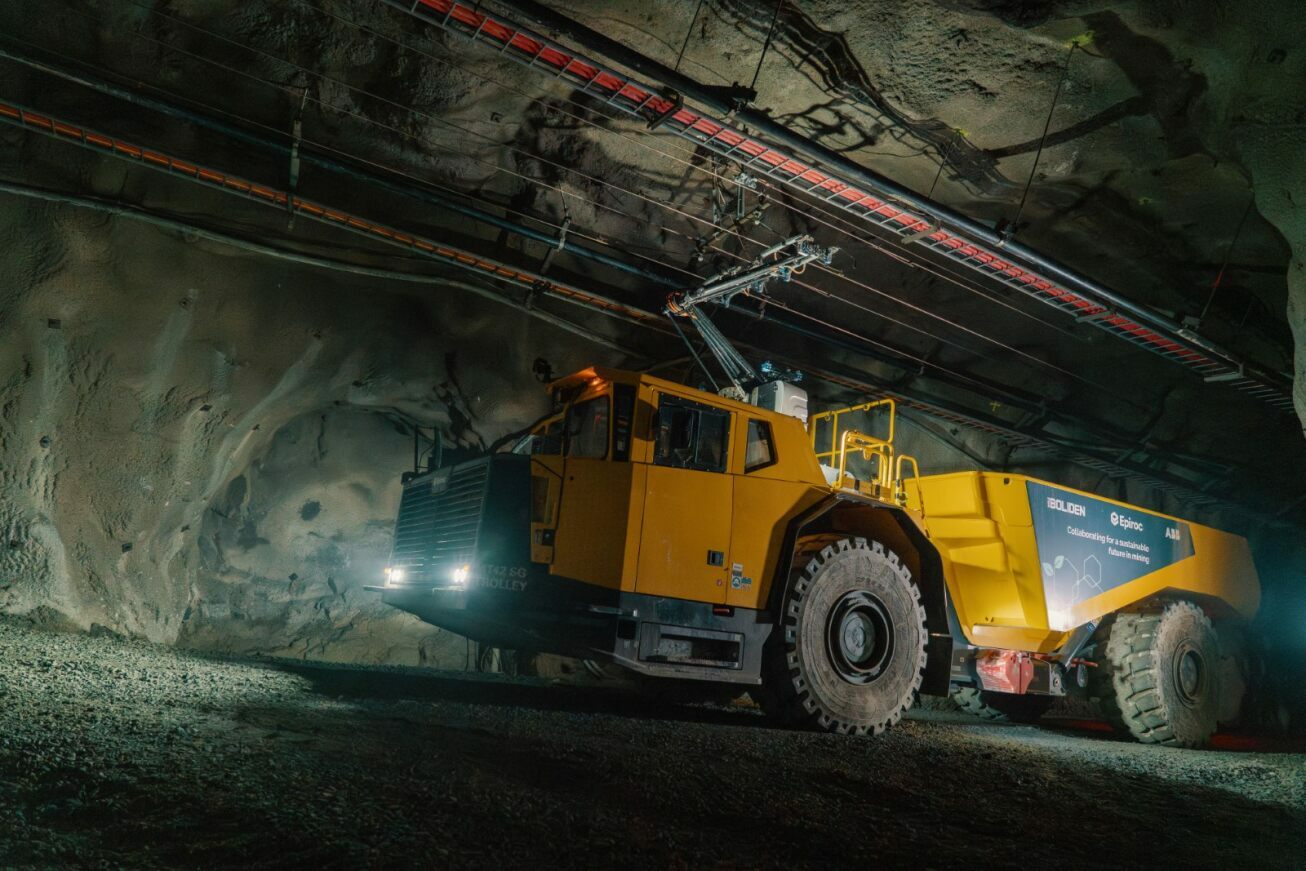
Mernok Elektronik, another acquisition, is a provider of collision avoidance systems for mines, to mitigate the safety challenge of noiseless electric equipment. While reduced noise and heat are advantages of electrification, some sort of warning system is necessary to keep workers safe. Epiroc is offering it to any other OEM that is interested. "We are not ringfencing the technology only for Epiroc," Sterley said.
Epiroc takes an ‘agnostic' approach towards the types of technology and infrastructure that will best enable electrification, as innovations continue to advance in areas such as battery technology. Customers can choose between a centralised unit that powers a drive train in their vehicle, or individual electric wheel motors, for instance. Overhead trolley lines have been cited by many as the best way to electrify haul trucks and are preferred by some. Sterley said: "Overhead trolley lines are not something that is new to the industry. They have been used extensively in surface mines with big haul trucks coming out of pits. But there are some small adjustments that need to be made to make work it underground." Epiroc has now achieved this through a partnership with ABB and Boliden.
As technology evolves, the company is seeking out new partnerships and acquisitions that will enable it to support customers in their sustainability journeys. "No company in the industry can go through the electrification journey by itself," Cloue said. "Partnership is a key and critical success factor."
Further partnerships on power generation and distribution are set to follow. "We also want to decarbonise our supply chain, meaning that we are working today to offer the greenest equipment on the market through collaboration with our suppliers," Cloue said. An example is a partnership with SSAB, a carbon-free steel manufacturer. Some Epiroc trucks are now being made from this carbon-free steel. Epiroc also works with Northvolt on battery recycling and has a battery-as-a-service scheme.
"We are not just providing electric equipment but looking at all the different possibilities for reducing the carbon footprint of our equipment and customers' operations," he said.