Lithium production stands at the forefront of the global shift toward renewable energy and electric mobility, powering everything from smartphones to electric vehicles. However, the journey from raw lithium brine to a market-ready product is a complex one, requiring a deep understanding of subsurface conditions and advanced lithium extraction systems.
SLB's extensive experience in developing technologies for the oil and gas industry gives SLB unparalleled expertise to develop, test, and deploy an integrated solution for sustainable lithium production solutions proven at scale.
The "well-to-product" integrated solution
To date, lithium extraction technologies address only specific challenges; the SLB solution addresses all the steps from finding the lithium reserve to the production of the battery lithium products. The SLB integrated solution uses innovative technologies to enable lithium extraction directly and continuously from brine, which is then purified and concentrated at the surface in a controlled, closed environment. This holistic lithium production process optimizes all the systems and technologies involved to minimize the use of land, water, energy, and chemical reagents to produce the high-quality, battery-grade lithium products.
The journey of lithium extraction encompasses several phases.
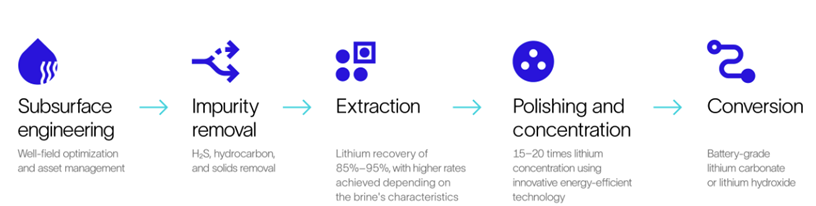
- Subsurface engineering: Understanding the geological formations and lithium concentrations is paramount to developing a successful project. SLB offers leading subsurface products to help identify the most promising lithium-rich zones using our basin modeling, efficiently developing the lithium reserve and producer well solutions using our static modelling, and finally modeling the reinjection of depleted brine using our unique dynamic modelling techniques. These solutions increase the reservoir performance while reduce the environmental impact of lithium extraction.
- Impurity removal: Initial treatment processes to prepare the brine for extraction. Pretreatment steps include filtration, as well as temperature and pH adjustments to ensure highest recovery in the extraction step.
- Extraction: Using direct lithium extraction (DLE) technology, this step extracts lithium ions from brine. The system can recover up to 96% of the lithium.
- Polishing and concentration: Using a precipitation and membrane system, this step removes the residual impurities and concentrates lithium eluate 15-25 times to create a lithium chloride ready for conversion to lithium carbonate or lithium hydroxide.
- Conversion: This is the final step required to transform lithium concentrate into a market-ready product. It involves chemical conversion processes to produce lithium carbonate or lithium hydroxide, which are the primary products used in battery manufacturing.
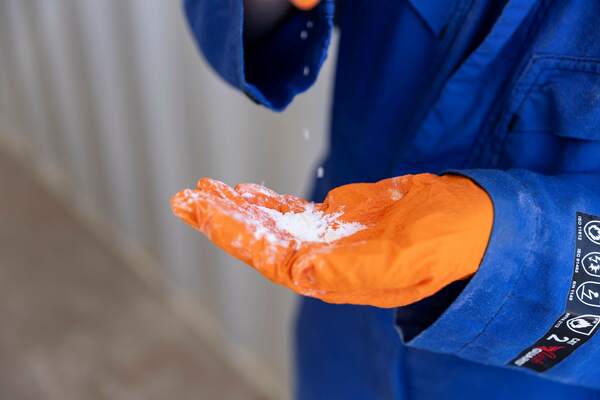
SLB's success story
Using integrated technologies, natural resource management, and improved process systems, SLB can produce battery-grade lithium products from brine in less than a day instead of months. This allows the industry to rapidly adjust production based on market pricing and demand and enables the development of lithium reserves in regions across the globe where lithium-rich brine may be found.
One of SLB's significant achievements in this field is the construction and operation of a demonstration plant in Clayton Valley, Nevada. This project provided invaluable lessons during commissioning and operation, necessitating modifications and redesign of key components to address challenges encountered when scaling up equipment to an industrial level. SLB's expertise in developing technology for extreme operating environments enabled a swift transition to a fully operational system, demonstrating the capability to adapt and innovate under real-world conditions.
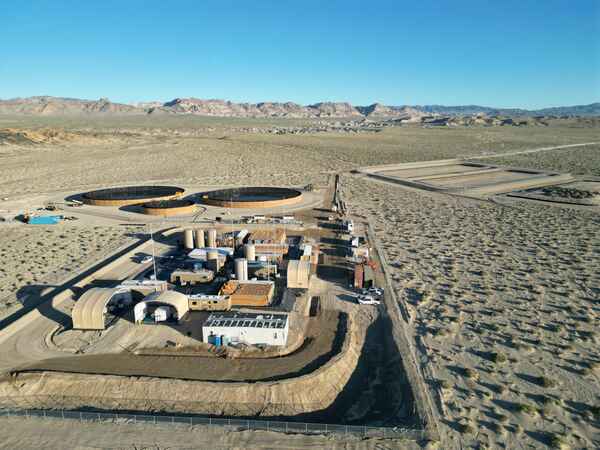
Key features that differentiate SLB's solution from traditional production methods:
- Speed to market: The SLB system is ready for engineering and deployment, thus allowing lithium asset owners to deploy commercial plants faster, while reducing the scaling risks.
- Improved economics: The solution integrates advanced technologies to enhance lithium extraction yield of over 90% — compared to less than 50% with conventional solutions — while reducing energy and chemical reagent consumption. At Clayton Valley, SLB achieved 96% lithium recovery rate with 98% impurity rejection in the DLE stage.
- Accelerated speed to market: The entire process, from extraction to conversion, takes hours, while the conventional evaporation process can take between nine to 18 months, depending on weather conditions.
- Enhanced sustainability: Sustainability is a core consideration in its offering. Minimizing land, power consumption, freshwater usage, waste streams, and chemical reagent consumption are all integral to the approach. The facility utilizes less than 10% of the land footprint of traditional methods. Sustainable water resource management also reduces water consumption by up to 95%. Spent brine is reinjected (after thorough testing) to minimize impact in high water stress and other sensitive environments.
By implementing the integrated process, SLB's customers can accelerate lithium production, extract more lithium, and minimize environmental footprint.
ABOUT THIS COMPANY
SLB
SLB is a global technology company that drives energy innovation for a balanced planet. We work each day on innovating, delivering digital at scale, decarbonizing industries, and developing energy systems
HEAD OFFICE:
- 5599 San Felipe St 8th Floor
Houston, TX 77056
United States - Phone: +46 8 456 11 00
- Email: sne@slb.com
- Web: www.slb.com/lithium
SOCIAL MEDIA: