With high recovery rates making for battery-grade nickel, reduced carbon emissions and lower operating and capital costs, Brazilian Nickel founder and technical director Anne Oxley is convinced that heap leaching is the future for the metal.
"We have always thought that," she told Mining Magazine. "We get recoveries around the 80% mark for nickel."
While commonly used in copper and in uranium with sulphuric acid, heap leaching is not widely used on a commercial basis with nickel.
However, it has significant advantages, both operationally and for sustainability. In the more usual high-pressure acid lead (HPAL) method for nickel, about 50% of the ore is discarded, Oxley said, because it isn't the right type of ore to go through the HPAL process. This results in large stockpiles of ore that cannot be used.
YOU MIGHT ALSO LIKE
Heap leaching also produces fewer carbon emissions and has lower operational costs.
Anne is one half of a husband-and-wife team that first started looking at heap leaching for nickel in 1999. They set up pilot projects at nickel projects in Turkey, the Philippines and, through cooperation with another company, in Colombia, before setting up their own enterprise and acquiring the Piauí Nickel Project in Piauí, the country's northeast region, from Vale in 2013. The sale was finalised in 2014 and they started the process of raising money.
"Piauí is the poorest state in Brazil," Oxley said. "There is not much mining there; it is mostly subsistence farming, so this is an important project for the area."
To boost the economy in the region, the state provides significant benefits to Brazilian Nickel, which is the largest employer in Piauí outside of the state. About 75% of employees are from the local area, and 35% are female. Partly as a result of this, it has gained Nickel Mark certification, an ESG accreditation which is related to the Copper Mark. The accreditation is the first awarded to any project in Brazil.
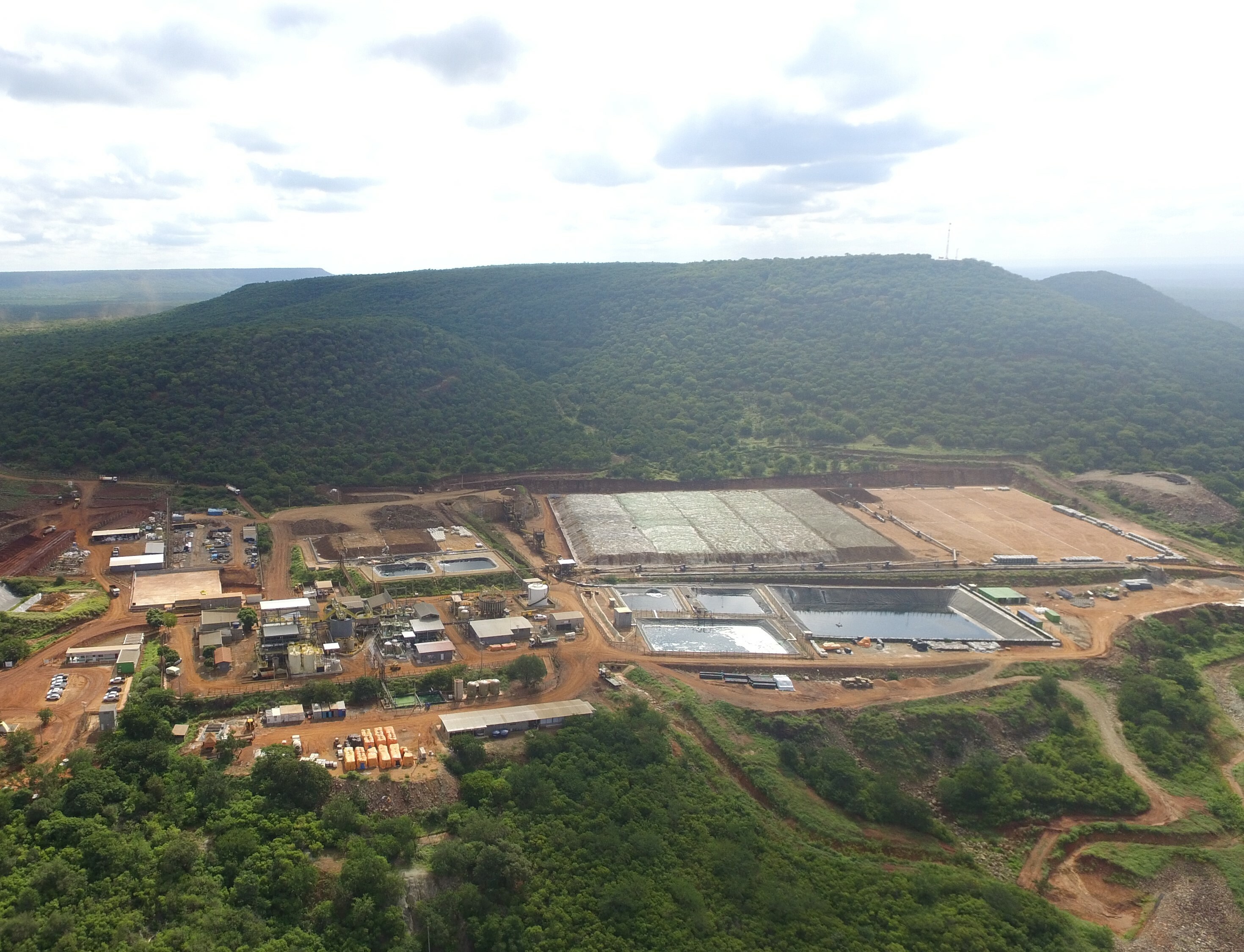
The first thing the Brazilian Nickel team did in Piauí to get the heap leaching process started was to build a demonstration plant. "We knew it worked, we just wanted to demonstrate it technically and get all the data we needed," Oxley said. After that plant was up and running, producing a few tonnes per month of nickel, they then built a small commercial operation, producing up to 1,000 tonnes per year in 2022. Experts from previous pilot operations were brought into the team.
"It was commercial proof of heap leaching," Oxley said. "It showed that people wanted the product and thought that it was, in the end, superior to other mixed hydroxide precipitates (MHPs).
"To this day, we have the most know-how in the world on nickel laterite heap leaching."
The process
Brazilian Nickel's heap leaching, developed over decades, differs slightly from other kinds of heap leaching. Firstly, very dilute sulphuric acid, similar in strength to some acid‐based household cleaning products, is slowly applied to crushed nickel ore on a lined pad to dissolve the nickel and cobalt contained in the rock in a several-month process cycle.
"Once the ore has been under the leach for a while, we do a recycle leach, and that creates an intermediate leach solution which is the bulk of the period," Oxley explained. "That keeps going for 180 days and builds up all the metals into the solution."
The team then takes that solution and puts that over the fresh ore, for three months. "That gives us an optimum solution that we feed to the downstream plant to treat, so that is our pregnant leach solution (PLS)."
This PLS has the lowest impurities and the highest value of nickel and cobalt, as well as the lowest acid possible. Minimising the amount of acid going to the plant reduces the amount of limestone used in the process.
"It's not like copper or gold, where you are just taking out the value metals," she said. "You have to leach the impurities out. We try and be very efficient in our process."
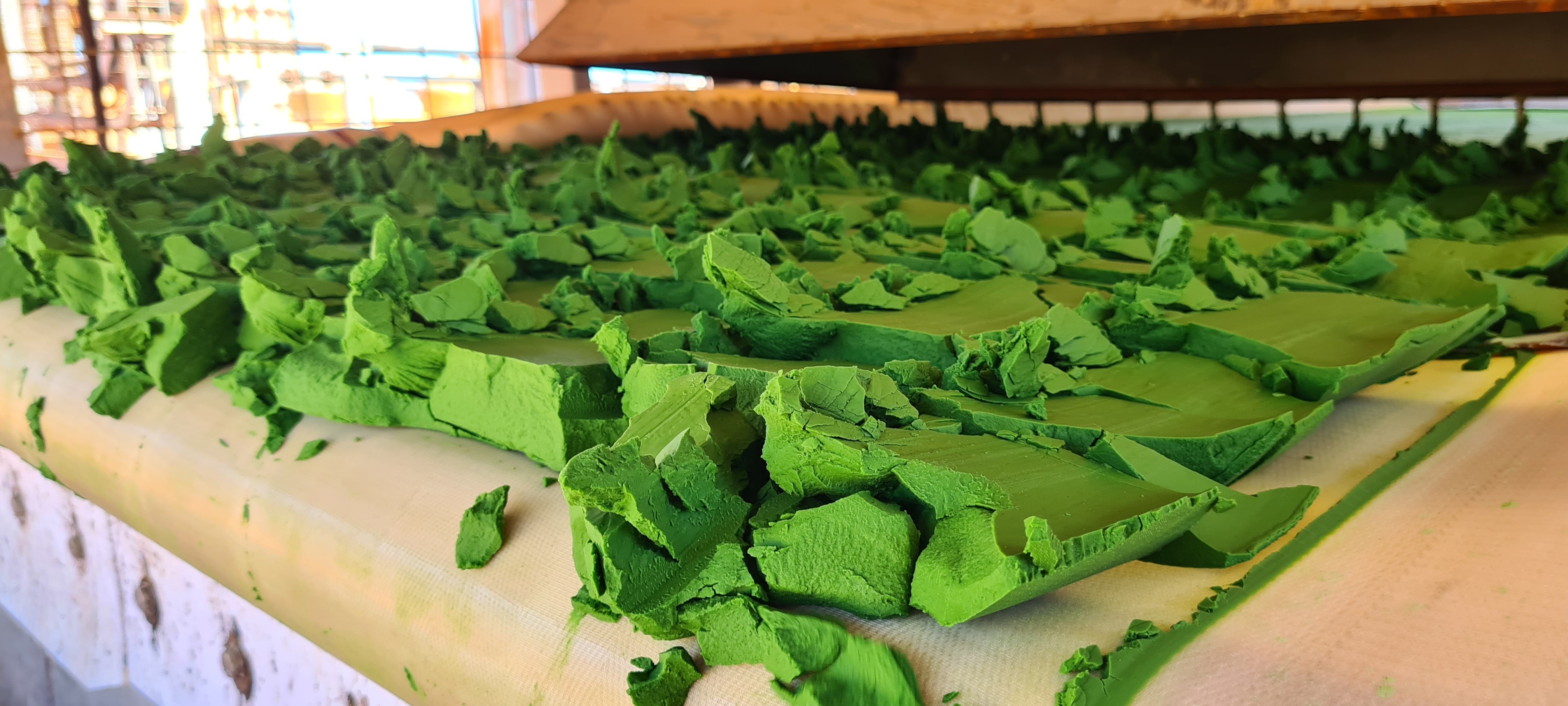
At the downstream plant, the pH of the solution is raised to remove further impurities, then an ion exchange is used to concentrate the nickel and cobalt solutions, and then excess manganese, magnesium and other impurities are finally removed with a much higher pH.
"Then all those solutions are recycled – it all goes back to the heap," Oxley said. "It's a closed loop for the solutions."
The resulting MHP contains about 50% of nickel on a dry basis, and about 2% cobalt, making it battery-grade.
One of the advantages is lower capital and operational costs than HPAL or other processing routes for nickel laterites. "It's not cheap, because nothing is, but it's significantly lower," Oxley said. "And it is lower CO₂."
Since more of the ore is suitable with heap leaching than with other methods, there is also less waste.
Favourable conditions
The state of Piauí is known for its dry, hot climate and large expanses of flat landscape, creating ideal conditions for heap leaching.
"The Piauí project does have good geological properties to make it low acid-consuming," Oxley said. "But we can do this anywhere."
The team at Brazilian Nickel have studied more than 40 nickel laterite deposits and believe that leaching is possible in all of them, albeit different locations will present different technical challenges.
"Magnesium is key because it's an acid consumer," she said. "Piauí has low rainfall, but it can still be done in areas like the Philippines with a lot of rain and wind. You just need to cover the heaps and manage water in a slightly different way."
As a hydrometallurgical process, heap leaching of course uses water but Brazilian Nickel recycles as much of the water it uses as possible. It is also working with Skarn Associates, a sustainability consultancy, to benchmark its water use against the industry.
Also notable is the fact that heap leaching leaves behind solid residues. This is particularly important in a country with its fair share of tailings dam disasters in its recent past, such as Mariana and Brumadinho.
The company has a progressive closure plan, undertaking rehabilitation measures as the project progresses.
The Piauí project is expected to go into production in 2028, with hopes that current nickel price volatility may have calmed by then.
New projects are already in the works, a joint venture in Brazil among them, but the company is also looking globally, despite its name, for other potential projects.