In 1804, a locomotive designed by Cornish engineer Richard Trevithick carried 10t of iron (and five wagons and 70 men) almost ten miles along the tram rails linking the Panydarren Ironworks and the town of Abercynon in Wales. With this journey, Trevithick's steam engine (and its load from a mine) launched the rail era and changed the world.
Two centuries on, the frenetic invention of the British rail engineers of the Industrial Revolution has quietened to a whisper—with an exception.
Today, Clayton Equipment is one of the UK's last domestically owned locomotive manufacturers.
Clayton has had many guises and owners in its near century of existence. Locomotives it built replaced the pit ponies in Welsh coal mines. It developed battery engines in the 1940s. And perhaps most remarkably, Clayton survived the destruction of the UK's domestic mining industry in the 1980s.
YOU MIGHT ALSO LIKE
While the UK's pits were closing, Clayton looked outward from its home in the Staffordshire town of Burton-on-Trent, intently focused on exports, and shipped hundreds of its locomotives to mines in more than 60 countries.
Clayton has built its name on its locomotives' endurance.
It maintains hard-working locos 40 years after they were first deployed, Clayton's sales and marketing director Mark Nolan told Mining Magazine, in an interview this month.
"It's an honour to be the last one standing," said Nolan.
But this storied company is not waiting for extinction. In fact, Nolan insisted that with Clayton's continued innovation, its future was "very bright".
Export driven
Nolan said that Clayton shipped its locomotives to Canada, Austria, the Philippines, and (in kit form) to China in 2024. In 2025, it will deliver locomotives to new markets, including Serbia, Egypt, Australia, and Saudi Arabia.
It is making a name outside the mining industry, landing a contract in Australia for a sugarcane producer and another for surface hauling in Egypt.
"We've got pure battery locos at Sellafield [nuclear power plant], which is difficult and is a nice feather in our cap," he said.
"The pipeline is very, very buoyant," said Nolan.
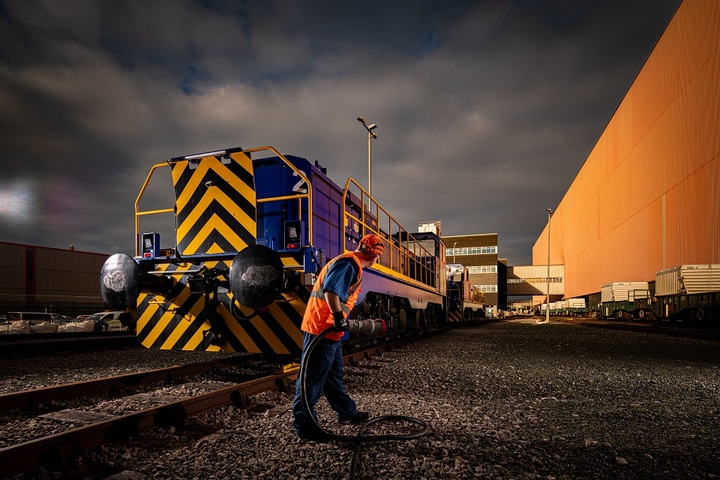
He said that Clayton's successes in one project will often lead to more contracts. "It creates a domino effect. We have to think about scalability, but that's in hand as well," he said. "So we're looking to expand the business."
Nolan said Clayton's export focus is "keeping the government happy". It works with the UK Department of Business and Trade (DBT) to find opportunities around the world - Nolan said that day he'd been chatting with DBT about a possible contract in Kazakhstan.
The UK is proud of its deep mining heritage and has world-leading expertise across the full mining lifecycle, including the manufacturing of mining equipment by well-established UK companies
A DBT spokesperson told Mining Magazine earlier this month (January 6) that it provides "vital support to UK companies both at home and abroad to succeed all over the globe via access to training such as through our Export Academy, information on export opportunities, activities such as trade missions and providing assistance on removing trade barriers."
"The UK is proud of its deep mining heritage and has world-leading expertise across the full mining lifecycle, including the manufacturing of mining equipment by well-established UK companies," said the spokesperson.
Making it special
With its team of about 15 engineers and 45 people in production, Clayton prides itself on building the right locomotive for their client's project.
"We design it from scratch to meet whatever requirements they want - which is a pain for me [as a salesman] sometimes!" said Nolan.
"We offer the full range of power drives, whether it's a diesel hybrid battery or battery with a pantograph to go on electrical catenary. And we do weights from 1.75t up to 150t," he said.
Nolan reeled off the types of locomotives Clayton has built—tunnelling locos, mining locos, and surface and mainline locos—and said that if needed, "we can make funicular railways."
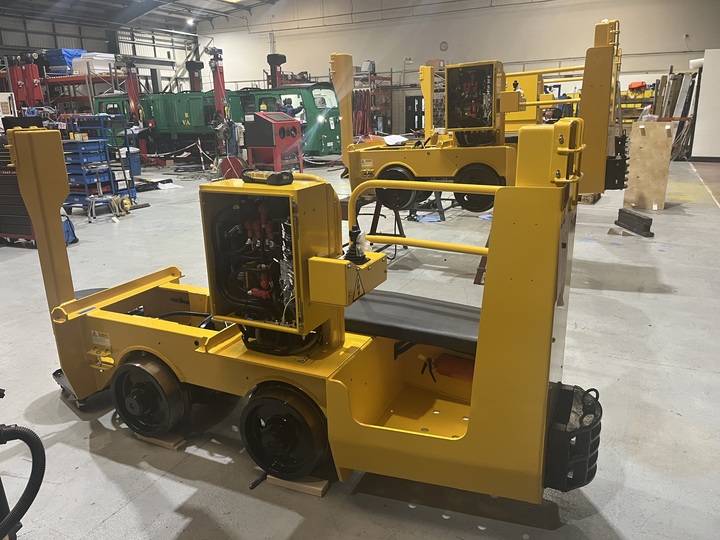
Once a specification is agreed upon and the customer approves the design, Clayton enters into a design freeze and begins to build the first model.
"From that point, it takes between nine and 12 months for the first one. But if they order multiples, they come in quick succession afterwards," he said.
When the locomotive is completed and shipped, Clayton provides full on-site training and technical support.
"We can also invite people during the manufacturing process to come and see the loco being manufactured, particularly if there are any aspects that are particularly relevant to them," said Nolan.
Batteries powering up
The mining industry has seen an uptick in demand for battery-run vehicles, but Nolan said that the specific conditions of a mine will still dictate the solution.
"I'm looking at a project now in the Philippines, which is a 90t loco. But it won't be battery, it'll be a hybrid," said Nolan.
Nolan said Clayton has moved away from offering standard lead acid to primarily using a thin plate pure lead (TPPL) battery. While it can supply lithium batteries, these are prohibitively expensive for a locomotive.
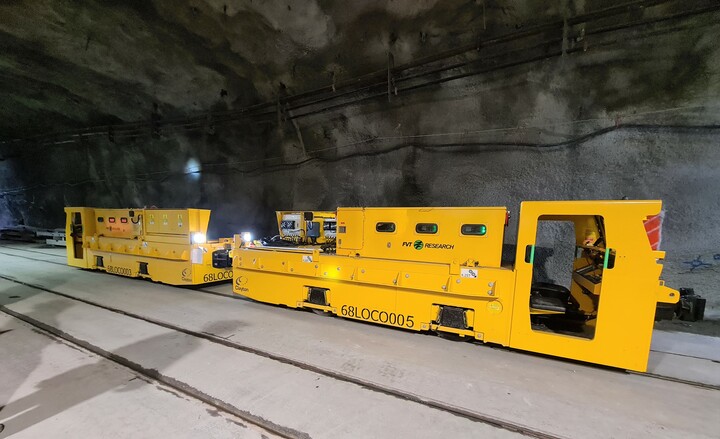
"The TPPL battery takes a very, very fast charge like lithium, it's maintenance free, and it's a lot less [expensive] than lithium. We supplied loco where the battery is worth more than the loco because of the lithium aspect of it," said Nolan.
Practicality is at the forefront of a mining company's decision-making, Nolan explained.
"These are generally workhorses. Mining companies aren't buying them for prestige or glamour. They are literally modern pit ponies," he said.
Made in China
Instead of shipping completed locomotives, Clayton produces "technology kits" for China's miners.
Not every Clayton locomotive is built in Burton.
To break into the huge Chinese market, it needed to adapt its manufacturing process to accommodate the country's domestic production rules.
Clayton's owner Steve Gretton had an established relationship with an engineering firm in China, which created an opportunity for the locomotive maker.
Instead of shipping completed locomotives, Clayton produces "technology kits" for China's miners.
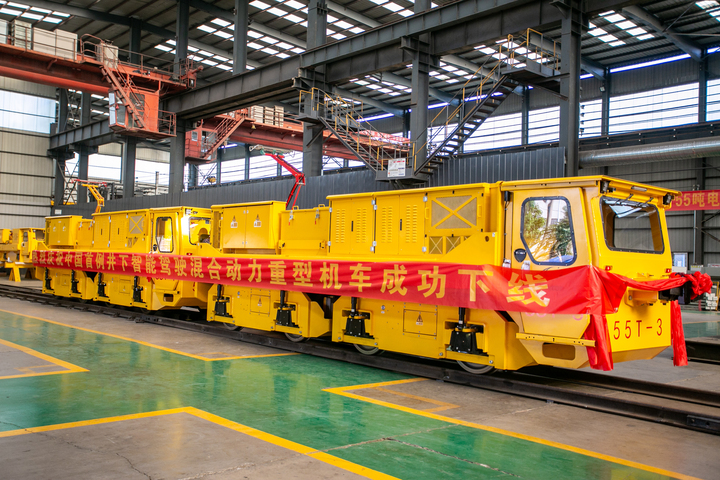
"We've developed different platforms in China that allowed us to send technology kits out into China, which they put together on their fabrication," said Nolan. "The technology, the drive, the drive train, and all the rest of it is produced in the UK. Then, we ship that over as a technology kit to be assembled in China."
The resulting locomotives are more cost-effective for the Chinese market while keeping the hard-won good name of Clayton.
"It keeps the technology and the quality there," said Nolan. "We've sent technical people out there to help them do the testing and commissioning and to make sure it carries the Clayton name."
The Eye of God
Clayton locomotives have remote operating capabilities built in as a standard. Any of its machines can be operated on a remote control from a station.
"I could sit here watch your mining loco go around wherever it's going, see the loading process, the unloading process, and monitor it all with a joystick at my desk," said Nolan.
But it's a Clayton monitoring technology called Loco Watch that excites Nolan most. Loco Watch is an Internet of Things (IoT) technology that relays real-time data through the cloud about how a locomotive is being driven and its general operating state.
A customer might get a notification to say that the machine was driven it too fast, or that its brake pads are wearing down, Nolan explained.
"We're also gearing this up, and we're very close to doing this with AI," he said.
Nolan said Loco Watch has been a hit with its customers.
"We don't just supply and forget"
At one underground mine, a locomotive driver overshot a barrier placed where minerals were meant to be dropped down—the error was "only by 30 cm," Nolan said.
"But we got on the IoT system and looked at the data, and we could say that he was going too fast around the corner," Nolan said - the driver's speeding made the overshoot inevitable.
The guys in [the mine] called it the Eye of God because it knew more than anyone else," he said. "That's particular to us. For safety, for return on investment, for productivity, it really helps deliver that to the client."
Loco Watch allows Clayton to do a lot of the maintenance remotely.
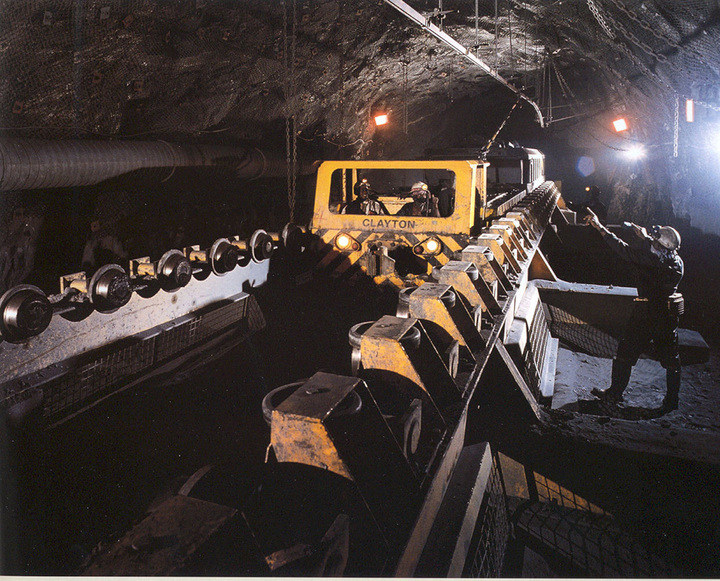
"Things like software changes or modifications to pneumatics, we can do that remotely from here, anywhere in the world," he said.
"We can tailor make the dashboard relevant to the department that's interested in it, whether it's parts supply and maintenance, safety, or a general manager who's running several mining locos in different tunnels," Nolan said.
The bounty of data gives it astonishing insight, with Clayton's engineers able to examine any incident retrospectively.
"We had [an incident] recently where a maintenance company put the wrong fluid in a battery. We could see that [had happened] through the battery performance," he said.
Theseus's locomotive
"We don't just supply and forget," Nolan said. He believes Clayton's pedigree is in large part built on the reputation its machines have for hardiness and durability.
"We've got locos out there that are 40 years old. Workhorses in some really, really difficult environments."
Clayton will provide new batteries and other parts, but Nolan said that "the fabrication and the fundaments of the loco are still the original ones".

The durability draws in clients, who feel safe knowing that the machine will be able to handle a mine's harsh environments.
"The mining company's main priority is to get mining done, to get iron ore, get gold, get copper," Nolan said. "So there's a lot of pressure on us to make sure that our loco delivers what we say it will."
Delivering is what Clayton's locomotives have done best and what has kept this British institution running over the long haul.