The idea of mines run entirely by robots has been around for decades - but experts say progress isn't fast enough despite the importance of successful robotics technology for our increasingly realistic prospects of extra-terrestrial mining.
Tim Anderson, senior manager specialising in mining and autonomy at Quartus Engineering, says robotic mining simply entails replacing human-controlled sensors and decision-making processes with machine-driven counterparts and that it needn't be that disruptive. Still, not enough miners are adopting it.
"The bulk of the mining machines - the electronics, hydraulics, structural mechanisms - don't change. What changes is how you control them. Do you control them from a cab inside the machine? Or from a remote station? And then how much of that control is human, and how much is automated (...) What you're trying to do is replace to the maximum extent possible."
"Think of a 20l water dispenser. The giant water bottle is all the technology we have at hand. But the mining industry is still taking it out in shot glasses and sipping it. A tremendous amount of capability that is not being leveraged (...) few people have integrated it all together."
YOU MIGHT ALSO LIKE
Anderson identifies three types of control mechanisms - remote, automated, and autonomous.
Remote control involves human operators directly controlling machines from another location using data links. Automation relies on pre-programmed algorithms to perform tasks, with minimal human intervention, while autonomy entails machines making decisions independently based on sensor data and AI algorithms.
For a fully robotic operation, you need synergy between all three types of control, according to Anderson - something that the mining industry has yet to achieve.
Greg Baiden, president of Penguin Automated Systems, a Canadian research and development company focusing on the implementation of robotic and automation solutions, agreed with this sentiment, saying that integrative approaches are key to robotic applications.
"The change to robotics will be pretty dramatic, in not only the equipment required but the methodology, production and organisational structures that need to be put in place. The mining industry right now has not yet got there. We're still kind of working on what I call islands of automation. You'll see scoop trends being run (...) but they're not integrated."
Sensors for autonomy
One of the key technologies driving robotic applications in mining are sensors, such as light detection and ranging (LiDAR) scanners, optical sensors, and gyroscopes.
These additions provide real-time data about the environment and equipment status.
In an October 2023 podcast with CXO talk, Caterpillar's chief technology officer, Karl Weiss, said that "LiDAR has been a key technology" for the company.
LiDAR scanners work by firing millions of laser pulses at a surface and measuring how long they take to bounce back. This data is then used to pain a detailed 3D picture of the site.
"The ability to look far enough in the distance and through a lot of different environmental distractions has been critical. The ability to capture millions of points per minute has given us the ability to have confidence of avoiding obstacles and staying on course."
"As we've evolved, we're using more and more camera technology and radar technology for different purposes to also watch different parts of the vehicle so that we can avoid other safety incidents that may not be straight ahead but beside the vehicle or in back. But all of this is dependent on connectivity to GNSS (satellites) and knowing where we are."
Similarly, Sandvik's Toro LH514 underground loader, a powerhouse in the AutoMine system, uses a suite of LiDAR scanners to paint a picture of the underground environment, enabling autonomous navigation and precise manoeuvring.
Gyroscopes, laser scanners and angle sensors act as its inner compass, maintaining stability and accuracy during loading, even on uneven terrain.
Optimising sensory data through AI
But while sensors have been used in autonomous operations for two decades now, processing sensory data through advanced algorithms, including artificial intelligence (AI) and machine learning is crucial to achieve fully robotic mining, according to Anderson.
"[First you can map] automatic things that happen that we do intuitively. But when you apply machine algorithms to that automatic sensing and intuition, then we have a pattern of something that's reliable and repeatable, and you're in a position where you can really take advantage of that," Anderson said.
Weiss noted that Caterpillar is also using sensor data to facilitate more efficient operations.
"[Our] transmission has several sensors in it, and we have the ability to take the data that we've collected over that 1.4 million assets and scan the data for anomalies to then be able to more proactively let our customer know that a problem may be occurring. Whether it's an operator operating in an unsafe way or whether it's a clutch that's going to wear out (...) we're able to catch those and speed up the information to our customer to save them downtime and a costly repair."
Facilitating datalinks
As the industry collects and processes more sensory data, there is a need to develop cohesive datalink systems that can connect and draw lines between various single agents, according to Anderson.
Datalinks are essentially transport mechanisms by which large volumes of sensor data are transmitted in real time between mining equipment and control centres.
"What makes or breaks cooperative architectures of multi-agent systems is data transport (...) We're in a time where we are we can collect so much data so quickly that bringing it all the way back to a remote transport system doesn't work because the data links don't support it. We're reaching a point where machines can take in more sensory information than people can and faster. So data transport begins to make or break these cooperative systems of machines in a distributed environment," Anderson said.
With 1.4 million connected devices, Weiss said that ensuring reliable data architecture is a core priority for Caterpillar.
"It's a scalable strategy when we talk about connected assets from connecting a very small piece of equipment for a lawn and garden care provider to this mining truck that is operating in an autonomous environment (...) For instance, in our mass amount of product, we are operating really in a cloud-native environment of where to store and process our data to this mine site where this massive amount of data has to be real-time (for obvious reasons around safety and performance). Those are on-premises data storage, and so we have a great team that does an excellent job of looking at the different needs of our customers along that spectrum."
Another company focusing on the creation of data architecture for mining is Huawei, whose Pangu Mine Model consists of a digital platform and integrated cloud infrastructure that can collect and synchronise data from autonomous mining operations.
Reliable equipment
Baiden said that critical to the development of robotic mining technology will be an industry shift from a 'until-failure' approach to more reliable equipment manufacturing.
"Mining today is based on a failure maintenance process," he said.
"We run the equipment until it breaks. In robotic mining, you must flip that philosophy. If something breaks, it's a very serious problem. For instance, you see in the news that a door that came off of a plane would get a high level of scrutiny. If this happened to a mining machine, nobody would care. But that philosophical change has to occur in the mining industry (...) Most mining equipment is not designed for high-reliability work, but that needs to change for autonomous operation."
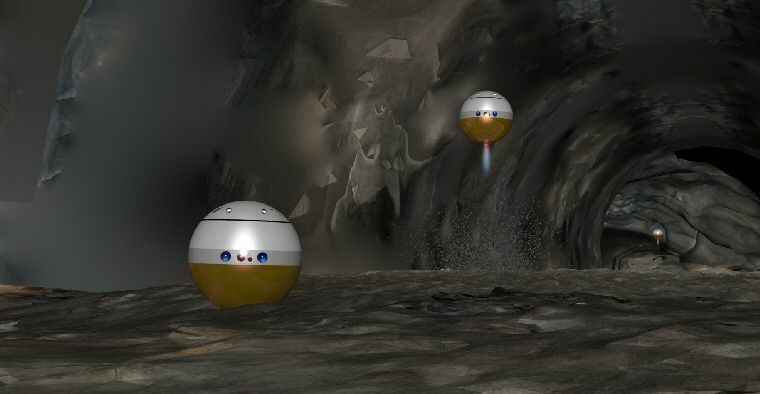
One operating system to rule them all
OEMs from across the globe are increasingly competing in the race towards a robotic future of mining. But the lack of a standardised operating system makes it difficult for diverse equipment from different vendors to communicate.
This lack of interoperability introduces friction in the adoption of these technologies, Anderson said.
"Almost every time I sit down with people, including miners such as Codelco, they say that they are running into this challenge where each individual vendor has its own way of implementing technology and controls, which don't talk to each other. And so, you either have to commit fully to all their machines, or there is a need to enforce a commonality standard so that all the machines can integrate into it."
Weiss similarly noted that Caterpillar has developed a standardised system for all its equipment: "As capabilities have improved, the ability to send and receive data in mass amounts at a reasonable price, and the computing capability to scan all of that data and make it useful, has transformed how we treat our data and how we have now standardized on putting telematics on all of our equipment as it leaves the factory so that we're able to help our customers be safer, more productive, and save money all at the same time."
While mining has yet to establish interoperable systems, an example of a strategy to streamline autonomous operations can be found in the maritime industry.
In particular, the US Navy has developed an unmanned maritime autonomy architecture (UMAA) system that aims to establish a "common interface and protocol, functional breakout to support standard component interfaces" and "standardised interfaces where commonality provides value", according to the Defence Logistics Agency.
Creating a culture fit
Another bottleneck to the development and adoption of robotic mining is the cultural shift required within the industry, according to Anderson.
Overcoming the perception that technology is complex and only for a select few is crucial. To do so, organizations need to invest in training and upskilling their workforce, fostering a culture of technological literacy and innovation.
"Somewhere along the line, we created this idea that math and science and technology is hard and it's only for a few special people (...) There's this idea that you've got to have a large team to be able to get through large amounts of technical capability and integrate it."
"There's a challenge for leadership in all these organizations that want to lean into the technical applications to turn to those people who maybe don't believe that they can really understand or have a deeper relationship with the technology and tell them that they are smart enough and that they shouldn't be intimidated by it."
Taking robots to the moon
An increasingly intriguing application of robotics is for lunar mining - something that is being explored by NASA and technology firms like Quartus Engineering.
"There's an interesting synergy between what current terrestrial miners do and what is going to be done in space. And in the middle, there's going to be some pretty innovative outcomes that are going to advantage the current mining industry. It will open new frontiers for us on Earth, as well as on the moon," Baiden, who is also the founder of Moonrise, a company specialising in space mining, and has previously worked with NASA on moon mining projects, said.
According to NASA's Jet Propulsion Laboratory, the moon "holds hundreds of billions of dollars of untapped resource", including rare earths and essential battery metals.
"[On the moon] we're going to need to do exploration, potentially with exploration drills. We're still going to need to make tunnels. We're still going to need to massively break rock - the transportation of that rock, the sizing of it and the equipment associated will be necessary. We'll need miniature versions of processing facilities,"
"[And all this must be done] by robots. What would happen is that we will go up with robots, but first we will experiment with those robots on Earth to create a fully robotic mine. And we're in the middle of looking at how we can set that up now."
But taking robots to the moon comes with a unique set of challenges, including the lack of gravity.
"There are efforts by people now looking to augment existing [mining] technology for the low gravity on the Moon. You could take a rover from Earth, but it won't be able to travel as fast because of the traction problem. So what can be done is making it heavier so it has more downward force," Jekan Thanga, associate professor at the University of Arizona, said.
"So far, there's been robotic excavation demonstrated on the Earth, under earth-like conditions. A few have demonstrated using lunar regolith simulations. Nobody has done it under 1/6th gravity yet."
Robots - from remote-controlled technology to fully autonomous operations - are inevitably at the crux of mining's future, particularly as we venture to the sky and seas, according to Baiden.
"Space mining is an application of robotic mining, and so is undersea mining. Underground and open pit mining are applications of robotic mining. And so at the heart of it all, going forward is robotic mining."