We all understand the significance of reaching a centennial milestone; it's a moment of fanfare, celebration, and recognition from the highest echelons of society. Orica has not only reached this landmark but has surpassed it, marking one hundred and fifty years of dedication to technology and innovation in the field of commercial explosives and blasting systems!
The company is refining its suite of blasting products, blending them with advanced digital solutions, aiming to optimise safety, productivity, recovery, and sustainability outcomes that meet the ever-evolving needs of the industry.
"Creating new digitally focused blasting techniques is not a task that can be rapidly or successfully achieved in isolation. That's why we are collaborating with our customers and other industry leaders to find solutions to our industry's biggest challenges and move towards a safer, more productive, and lower-carbon future together," outlines Nigel Pereira, Vice President - New Technology Commercialisation
"Partnering with industry leaders who are experts in areas across the mining chain, other than blasting, enables Orica to develop technology to integrate workflows that can improve the performance of the whole mine."
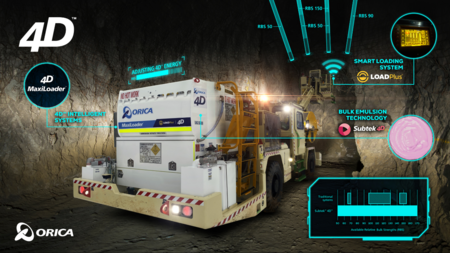
Orica is notably advancing several systems with advanced digital backbones, blending their industry-leading explosives expertise with modern technologies for improved outcomes.
A great example of this is the 4D™ bulk explosives technology, which enhances blast control with precise, adaptable energy application across a wide range of geological settings. It overcomes traditional limitations by using emulsion chemistry and digital control technologies, allowing for instant energy adjustments within individual blast holes.
Mining engineers can tailor energy profiles to specific parts of their mine, with easy implementation by charge crews through a simple user interface. The automated, repeatable LOADPlus™ system ensures accurate explosives placement, leading to predictable outcomes.
"Orica Digital Solutions employs a development partnership methodology to collaborate with forward-thinking operators to create purpose-driven solutions," Matt Craft, Senior Manager - Technology Blast Design & Execution.
"This proactive partnership approach ensures the team aligns with customer requirements and removes any product- market fit risks. Central to our digital product solutions is the emphasis on data-driven decision-making, which may come in many forms, all converging towards actionable opportunities."
Dugald River was the first mine globally to trial Orica's Subtek™ 4D™ system for underground. MMG and Orica worked together in a multi-phase trial to explore the effects of the wider energy range and variable in-hole energy control. Orica operations personnel loaded blast holes in conjunction with MMG employees, and contractors, while Orica technical services engineers provided guidance on design and engineering solutions.
This technology delivered impressive results when compared to a baseline of traditional stope firing techniques. Most notably from the findings was a reduction in stope hanging wall failure by a factor of >60%, which makes a huge impact on downstream material movement and processing requirements.
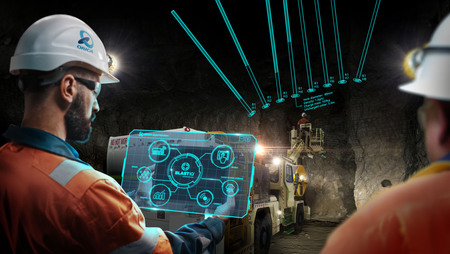
Orica's new BlastIQ™ Underground complements the 4D™ technology by digitising the drilling QA/QC, hole prep, and loading requirements that support an optimised 4D™ blast. BlastIQ™ Underground is a pivot from the popular surface variant, which is a packaged, easy to deploy ecosystem of products including a powerful next generation design app, autonomous cloud synchronisation, infield mobile application, raw data access, document storage, and web-based data analytics.
With an emerging suite of digitally focused blasting solutions emerging onto the market and an amplification of Orica's position as a global leader in underground blasting innovation, the question may be, what is next?
Orica believes automation will likely be a key emerging trend in addressing the future industry wide challenges of obtaining safe access to challenging orebodies due to the increasing demand for critical minerals.
The first phase of automation will focus on improved safety, by reducing the exposure of workers to hazardous and risky situations, such as dust, noise, rockfalls and explosives.
"Artificial Intelligence will play a critical role towards enhancing the decision-making process for automated blasting systems. We are already seeing the value of machine vision in managing variables on bench and these systems will only integrate further into blast automation to deliver enhanced productivity of the whole blasting process" states Pereira.
Orica is currently investing in the next generation of digital solutions that will seamlessly connect our customers' physical and digital worlds so they can readily understand and optimise their operations at every step of the value chain, from exploration to processing.
In closing, Craft shared the following, "We are focusing on key emerging technologies like procedural streaming, cloud computing, modern programming frameworks, development security operations, and AI/ML. These are central to solving our customers' challenges in this era of rapid technological change. We're carefully selecting technologies that best address critical customer problems and these systems will only integrate further into blast automation to deliver enhanced productivity of the whole blasting process."
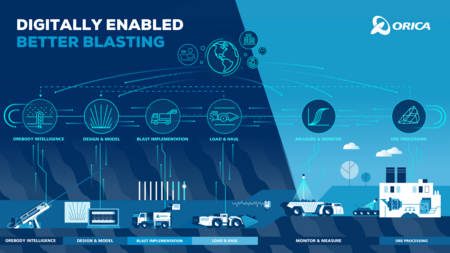
Orica, after 150 years in business, is delivering incremental and stepped change technologies for those working within the mining sector. Whilst AI may have been only a figment of the imagination when the business emerged, it is now a tangible next step in meeting their global customer base's needs both above and below ground.