In an effort to reduce their operating costs and environmental footprint, miners are increasingly turning to HPGR technology as an alternative to energy-intensive tumbling mills. However, in instances where operators are reluctant to move away from legacy equipment, their primary concern is that it might impact equipment availability, resulting in lost production.
In terms of HPGRs specifically, pre-mature bearing failures have plagued some OEMs, which has caused some operators to be wary of the technology.
But Weir believes that these premature bearing failures are a consequence of some poor design choices. In contrast, the design fundamentals that underpin its ENDURON® HPGR have proven to deliver unrivalled HPGR availability without compromising grinding efficiency.
Indeed, Weir is so confident of this that it's offering a 10-year (100,000 hours) guarantee on its bearing arrangement.
Causes of Premature bearing failure
The primary reason for premature bearing failure is unfavourable lubrication conditions as a result of grease or oil contamination and/or lubrication breakdown caused by excessive bearing temperatures.
Contamination commonly occurs when the sealing lips open when the rollers skew, resulting in dirt ingress. This contaminant acts like an abrasive grinding paste, causing high temperatures, accelerating wear and, ultimately, leading to bearing failure.
Another common cause of high bearing temperatures is insufficient cooling. High temperatures reduce oil viscosity, which reduces lubricant film thickness. This, in turn, increases friction, which generates heat, resulting in shorter bearing life.
Moreover, failure is often the result of unbalanced bearing load distribution, which causes bearing edge loading. This can be overcome by ensuring there's a full line contact across the roller bodies.
Unrivalled availability
Firstly, roller skewing is a non-negotiable attribute to accommodate load balancing and to maximise size reduction. It's also an essential feature to ensure the HPGR can adapt to the monthly – or even daily – feed variations of mineral processing plants.
The ENDURON® HPGRs' bearing arrangement skews with the roller, ensuring the seals aren't ‘opened up' and thereby preventing contaminant ingress. This is achieved with the fully controlled oil lubrication system, which ensures the lubrication remains clean and the bearings remain at a constant temperature.
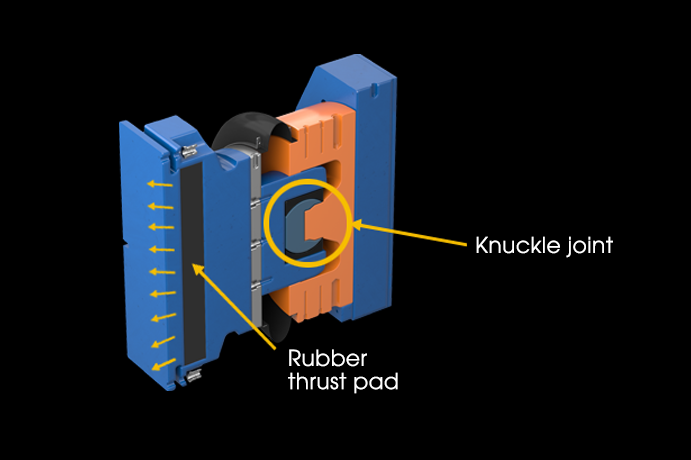
Moreover, the internal knuckle joint within the single side hydraulic cylinder aligns during roll skew, generating hydraulic press force, while the rubber thrust pad distributes the loads evenly across the bearing arrangement and avoids ‘hard contact'. Radial and axial loads are separated and distributed across both four-row cylindrical bearing configuration and axial thrust bearing.
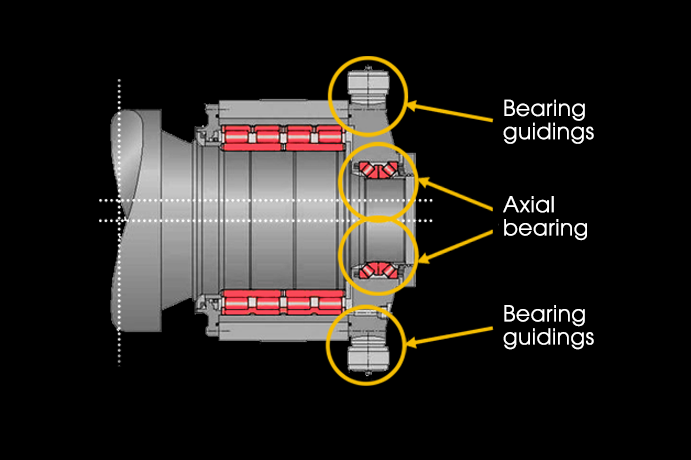
In contrast, other OEMs use spherical bearings to absorb both axial and radial loads.
Another important feature of the ENDURON® HPGR is that the bearings remain in line with the position of the roller during skew as bearing guidings are engineered outside of the main frame, allowing the bearings to swivel.
Reduced complexity
Greenfield mines are increasingly located in remote regions, while the ore bodies are becoming less homogenous and more complex to process. To combat these challenges other OEMs have opted for more complex flanged tyre designs on their HPGRs; however, this complexity increases operational risk, often leading to unplanned bearing failure and, as a result, unscheduled downtime and lost production.
Under these challenging conditions, Weir has, instead, opted to minimise operational complexity. The design fundamentals that underpin its ENDURON® HPGR provide greater flexibility and, ultimately, more operational certainty and equipment availability.
To find out how to take advantage of Weir's 10-year (100,000 hours) ENDURON® bearing guarantee click here.
ABOUT THIS COMPANY
Weir
With world class engineering expertise, Weir works in partnership with our mining customers to solve their operating challenges safely, efficiently and sustainably.
CONTACT DETAILS:
- Website: http://www.global.weir/
- Email: https://www.global.weir/contact-us/